Commercial Roofing Systems: Selection, Installation, and Maintenance
May 7th, 2025
10 min.
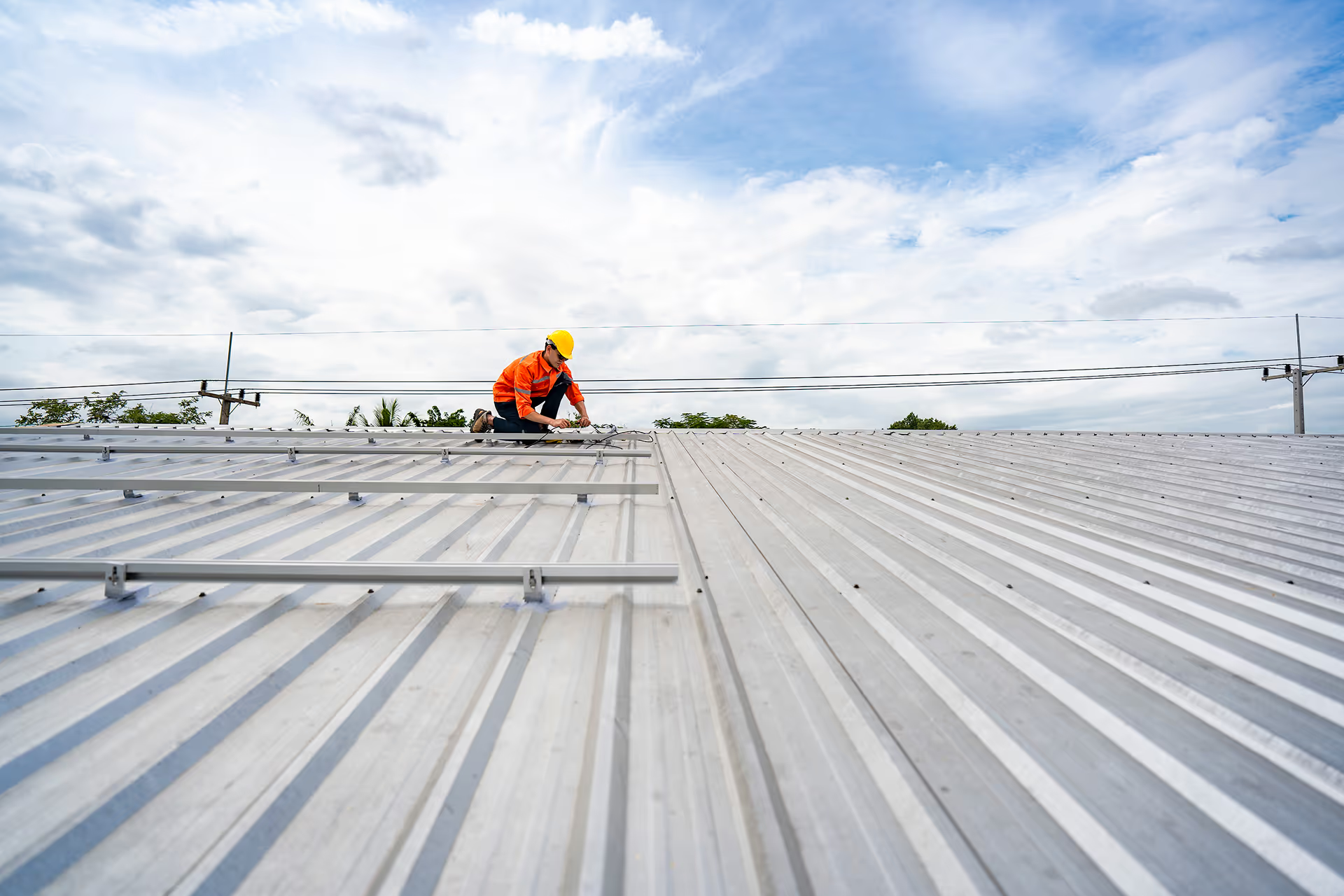
When it comes to protecting your business investment, few decisions are as critical as selecting the right commercial roofing system. At King Construction, we've spent decades helping property owners navigate the complex world of commercial roofing systems, understanding that the right choice can mean significant savings in energy costs, maintenance expenses, and overall building protection. Commercial roofing systems differ substantially from residential options in scale, materials, and installation techniques. Whether you're constructing a new facility or replacing an aging roof on your existing property, understanding the fundamentals of commercial roofing will empower you to make informed decisions that protect your business building roof options for years to come. This guide will walk you through the essential considerations in selecting, installing, and maintaining the ideal roofing solution for your commercial property.
Selecting the Right Commercial Roofing System
The first step in selecting the appropriate commercial roofing system is understanding the primary options available on today's market:
Built-Up Roofing (BUR): One of the oldest and most reliable commercial roofing systems, BUR consists of alternating layers of bitumen (asphalt) and reinforcing fabrics, creating a finished membrane. These systems are known for their excellent waterproofing and durability.
Modified Bitumen: This evolved form of BUR uses factory-fabricated layers of asphalt modified with polymers for increased flexibility and strength, particularly in cold temperatures.
Single-Ply Membranes: These include popular options like TPO (Thermoplastic Polyolefin), PVC (Polyvinyl Chloride), and EPDM (Ethylene Propylene Diene Monomer). Single-ply systems have gained significant market share due to their lightweight nature, installation speed, and energy efficiency.
Metal Roofing: Perfect for buildings requiring longevity and minimal maintenance, metal roofing systems can last 40+ years when properly installed. For more information about metal roofing, read our article, "Metal Roofing for Commercial Buildings: Durability and Performance".
Spray Polyurethane Foam (SPF): A monolithic, seamless roofing system formed by mixing liquid components that expand to form foam, then covered with a protective coating.
Green Roofing Systems: An increasingly popular sustainable option featuring living vegetation installed over a waterproofing membrane. These systems provide excellent insulation, stormwater management, and environmental benefits.
Flat Roof Solutions: For buildings with minimal slope, specialized systems like EPDM, TPO, and PVC offer excellent protection against ponding water. Learn more about the benefits of flat roofing in our article, "Flat Roof Solutions for Commercial Properties".
Key Selection Factors
When evaluating commercial roofing systems for your property, consider these critical factors:
- Building Structure and Design: Your building's structural capacity determines which roofing systems are feasible. Heavier options like BUR require stronger structural support compared to lightweight single-ply membranes.
- Climate Considerations: Local weather patterns significantly impact roofing performance. In hot, sunny climates, reflective roofing materials reduce cooling costs. In areas with high precipitation, superior waterproofing becomes essential.
- Budget Constraints: Initial installation costs vary widely among commercial roofing systems, but it's crucial to evaluate the total lifecycle cost, including maintenance, repairs, and expected lifespan.
- Energy Efficiency Goals: Modern commercial roofing systems can dramatically impact building energy performance. Cool roofs reflect solar radiation, reducing cooling demands, while insulated systems minimize heat transfer in all seasons.
- Local Building Codes: Regulations often dictate minimum requirements for fire resistance, wind uplift resistance, and energy performance of commercial roofing systems.
- Sustainability Objectives: If environmental impact is a concern, consider recycled content materials, recyclability at end-of-life, and options like solar-ready or vegetative roofing systems.
- Warranty Coverage: Manufacturer warranties for commercial roofing systems vary significantly in duration and coverage scope. Some cover materials only, while others include labor for repairs.
Cost-Benefit Analysis
At King Construction, we recommend conducting a thorough cost-benefit analysis before making your final decision. The right commercial roofing system balances upfront costs with long-term value. Consider:
- Initial Installation Cost: Materials and labor for installation
- Expected Lifespan: How long before replacement becomes necessary
- Maintenance Requirements: Annual costs of keeping the roof in optimal condition
- Energy Savings: Potential reduction in heating and cooling expenses
- Insurance Implications: Possible premium reductions for more durable systems
For example, while a TPO single-ply membrane might have a lower initial cost than a metal roofing system, the metal option's significantly longer lifespan (often 40+ years versus 20-25 for TPO) might provide better long-term value despite the higher upfront investment. Similarly, business building roof options that offer superior energy efficiency may cost more initially but deliver substantial operational savings over time.
Professional Installation Practices
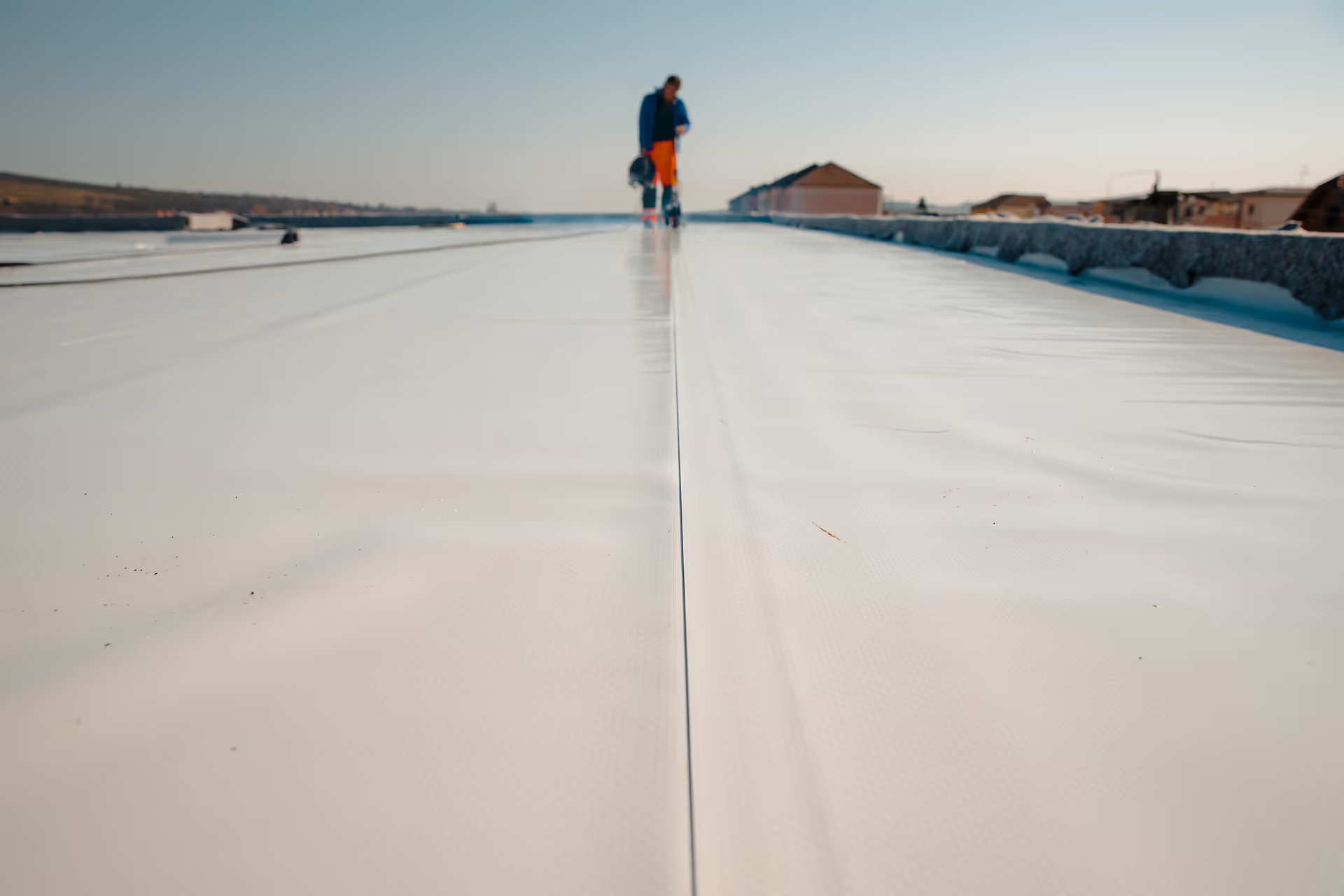
Proper installation begins well before the first material arrives on-site. At King Construction, our professional installation process includes:
Comprehensive Roof Assessment: For replacement projects, we thoroughly evaluate the existing roof condition, identifying underlying issues that must be addressed before installing new materials.
Detailed Project Specifications: We develop precise specifications tailored to your building's unique requirements, including material selections, application methods, and quality control procedures.
Strategic Scheduling: Commercial roofing installation requires careful coordination with business operations to minimize disruption. We develop timelines that account for weather conditions, business activities, and material lead times.
Safety Protocol Development: Roofing installation presents significant safety challenges. We establish comprehensive safety plans addressing fall protection, equipment operation, material handling, and emergency procedures.
Permitting and Compliance: We manage the often-complex process of obtaining necessary permits and ensuring compliance with local building codes and regulations.
Installation Techniques for Different Systems
Each commercial roofing system requires specialized installation techniques to ensure optimal performance:
Built-Up Roofing Installation: Multiple layers of bitumen and reinforcement fabrics are meticulously applied in overlapping layers. Hot bitumen application requires specialized equipment and highly trained crews to ensure proper adhesion between layers.
Single-Ply Membrane Installation: These systems can be fully adhered, mechanically attached, or ballasted. Each method requires precise attention to seam creation, as proper seaming is critical to system integrity.
Metal Roofing Installation: Proper panel alignment, fastener selection, and flashing details are essential for metal roofing performance. Expansion and contraction accommodation is particularly important for these systems.
Spray Foam Application: SPF systems require specialized equipment and highly controlled application conditions. Temperature, humidity, and wind conditions must all fall within acceptable ranges for proper foam formation and adhesion.
Green Roof Installation: These sophisticated systems involve multiple components, including waterproofing membranes, root barriers, drainage layers, growing media, and vegetation. Each component must be carefully installed in the proper sequence.
Quality Control Measures
Professional installation includes rigorous quality control throughout the process:
- Material Verification: Ensuring delivered materials match specifications and are free from manufacturing defects.
- Installation Monitoring: Continuous supervision by experienced project managers who verify adherence to manufacturer guidelines and project specifications.
- Seam Testing: For single-ply systems, physical testing of seams ensures watertight connections.
- Moisture Surveys: Electronic scanning can detect trapped moisture in the system before completion.
- Final Inspection: Comprehensive evaluation of the completed commercial roofing system before project closeout.
- Documentation: Detailed records of materials used, installation methods, and quality control measures provide valuable references for future maintenance.
Warranty Considerations
Quality installation directly impacts warranty coverage. When selecting a commercial roofing contractor, ensure they are:
- Manufacturer-Certified: Many premium warranty options are only available through certified contractors.
- Properly Insured: Comprehensive insurance protects you from liability during the installation process.
- Experienced: Look for contractors with specific experience installing your chosen system.
At King Construction, we maintain certifications with major roofing manufacturers, allowing us to offer the industry's most comprehensive warranty options for commercial roofing systems.
Maintenance Strategies for Longevity
Even the highest quality commercial roofing system requires ongoing maintenance to achieve its full potential lifespan. At King Construction, we emphasize proactive maintenance as the most cost-effective approach to roof management.
Scheduled Inspection Programs
Regular inspections form the foundation of effective maintenance. We recommend:
Bi-Annual Professional Inspections: Comprehensive evaluations conducted by qualified roofing professionals in spring and fall to identify and address seasonal damage.
Post-Event Inspections: After severe weather events, construction activities, or HVAC installations, targeted inspections identify potential damage.
Documentation Systems: Maintaining detailed records of all inspections, including photographs of roof conditions, creates valuable historical documentation of roof performance.
During professional inspections, experienced technicians evaluate:
- Membrane condition (blistering, ridging, splitting, or deterioration)
- Seam integrity
- Flashing conditions at penetrations, edges, and transitions
- Drainage system functionality
- Signs of water infiltration
- Attachment stability
- Surface deterioration from environmental exposure
Common Maintenance Tasks
Regular maintenance of commercial roofing systems typically includes:
Debris Removal: Clearing leaves, branches, and other debris that can trap moisture and accelerate deterioration.
Drainage Maintenance: Ensuring gutters, downspouts, and internal drains remain clear and functional.
Sealant Inspection and Replacement: Checking and replacing deteriorated sealants at flashings, penetrations, and terminations.
Minor Repair Execution: Addressing small issues before they develop into significant problems.
Protective Coating Application: For applicable systems, reapplying reflective or protective coatings at manufacturer-recommended intervals.
Vegetation Control: For buildings near trees, removing encroaching branches and controlling roof-top vegetation growth.
Extending Roof Lifespan
Beyond basic maintenance, several strategies can significantly extend the life of commercial roofing systems:
Roof Coating Systems: Applying specialized coatings can rejuvenate aging roofs, increase reflectivity, and enhance waterproofing. Options include:
- Acrylic coatings for UV protection and reflectivity
- Silicone coatings for superior waterproofing
- Aluminum coatings for heat reflection and UV protection
Targeted Reinforcement: Adding additional protection to high-traffic areas or zones with concentrated mechanical equipment.
Performance Monitoring: Implementing moisture detection systems or regular thermographic scanning to identify problems before they cause significant damage.
Preventative Repairs: Addressing early signs of deterioration before they lead to system failure.
Developing a Maintenance Budget
Effective budgeting for commercial roofing maintenance typically follows this formula:
- Routine Maintenance: Annual allocation of approximately $0.10-$0.15 per square foot for regular inspections and minor repairs.
- Periodic Restoration: Budgeting for major maintenance interventions (coating applications, partial replacements) at 7-10 year intervals, typically costing 25-35% of replacement value.
- Emergency Fund: Setting aside reserves for unexpected damage requiring immediate repair.
This proactive approach to maintenance budgeting typically reduces the total lifecycle cost of commercial roofing systems by 30-50% compared to reactive maintenance strategies.
Advanced Considerations for Modern Commercial Roofing
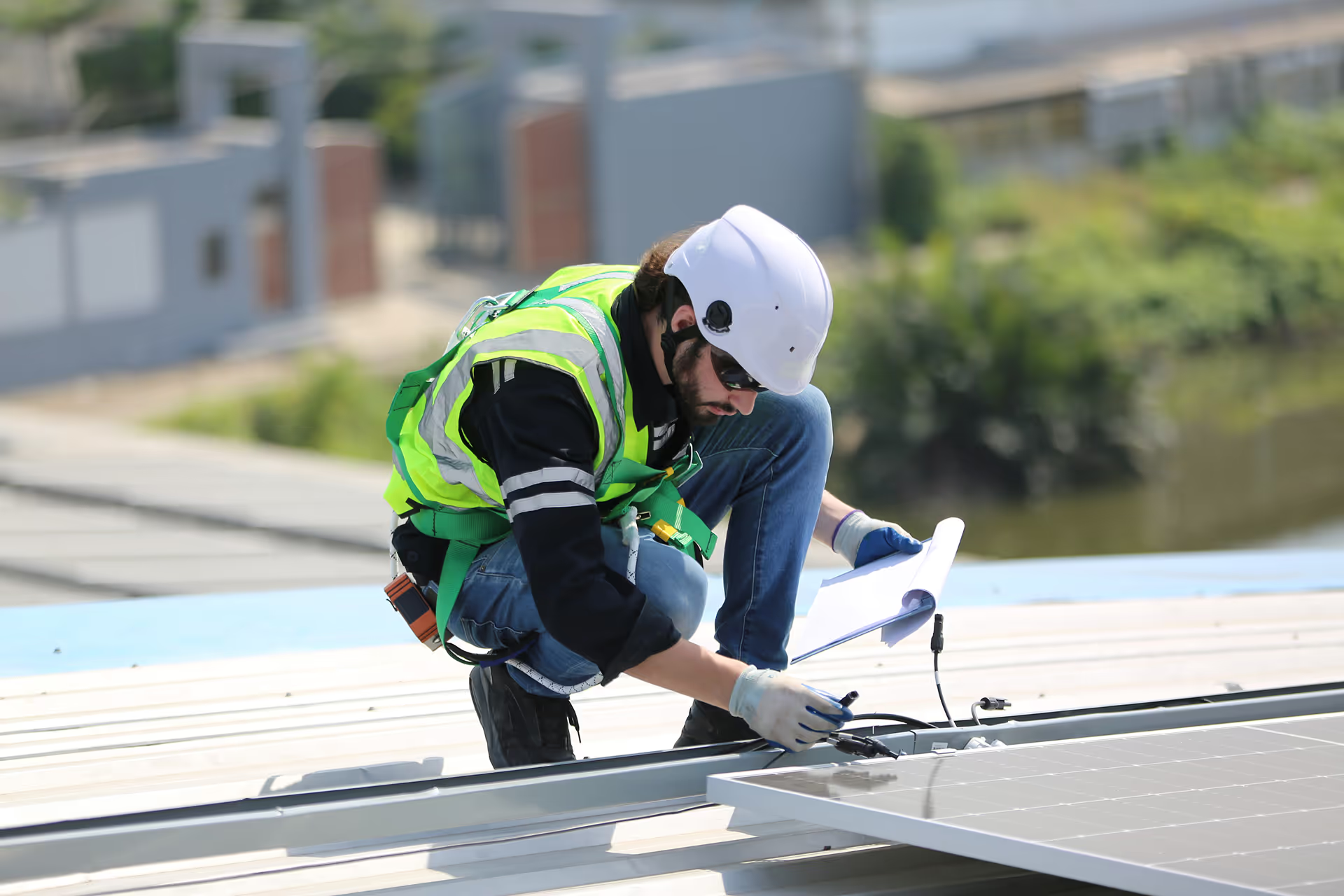
Modern commercial roofing systems increasingly focus on energy performance. Key innovations include:
Cool Roofing Technology: Highly reflective surfaces that minimize heat absorption, reducing cooling costs in warm climates. These systems can reduce roof surface temperatures by up to 60°F compared to traditional dark roofing.
Enhanced Insulation Systems: High-R-value insulation incorporated into commercial roofing systems significantly reduces heat transfer, improving building energy efficiency in all seasons.
Photovoltaic Integration: Many modern commercial roofing systems are designed for seamless integration with solar panel arrays, allowing buildings to generate renewable energy while maintaining roof integrity.
Advanced Ventilation: Engineered ventilation systems that work in harmony with the roof assembly to reduce heat buildup and moisture accumulation.
Sustainability Considerations
Environmental impact has become a significant factor in commercial roofing system selection:
Recycled Content Materials: Many roofing manufacturers now offer products containing significant percentages of recycled materials, reducing environmental impact.
End-of-Life Recyclability: Some systems, particularly single-ply membranes and metal roofing, can be recycled at the end of their useful life rather than contributing to landfill waste.
Reduced Environmental Impact: Low-VOC adhesives and installation methods minimize air quality impacts during installation.
Green Roof Benefits: Living roof systems provide habitat creation, stormwater management, air quality improvement, and urban heat island reduction.
Technological Advancements
The roofing industry continues to evolve with advanced technologies enhancing performance:
Smart Roof Monitoring: Electronic systems that continuously monitor roof conditions, alerting building owners to leaks or performance issues in real-time.
Drone Inspection Capabilities: Advanced imaging technology allows for detailed roof evaluation without requiring physical access to all roof areas.
Predictive Analytics: Software tools that use historical performance data to predict maintenance needs and optimize roof management strategies.
Advanced Weather Resistance: New material formulations providing enhanced performance in extreme weather conditions, including high winds, hail, and temperature fluctuations.
Regulatory Compliance
Commercial roofing systems must increasingly comply with evolving regulations:
Energy Code Requirements: Many jurisdictions now mandate minimum reflectivity and insulation values for commercial roofing systems.
Wind Uplift Resistance: Enhanced standards for wind performance, particularly in hurricane-prone regions.
Fire Resistance Classifications: Stringent requirements for roof assembly fire performance, especially in wildfire-vulnerable areas.
Chemical Restrictions: Regulations limiting certain chemical compounds previously common in roofing materials.
At King Construction, we stay current with these advanced considerations, ensuring our clients receive commercial roofing systems that not only meet today's standards but are positioned to perform well into the future.
Conclusion
Selecting, installing, and maintaining the appropriate commercial roofing system represents one of the most significant decisions facing property owners. The right system protects your building assets, contributes to energy efficiency, and provides decades of reliable performance when properly maintained. By understanding the distinctive characteristics of various commercial roofing systems, implementing professional installation practices, and committing to proactive maintenance, you can maximize your roofing investment's value.
At King Construction, we've guided countless commercial property owners through this process, delivering tailored roofing solutions that align with their specific building requirements, budget constraints, and performance expectations. We understand that each commercial property presents unique challenges and opportunities, requiring individualized approaches rather than one-size-fits-all solutions.
Whether you're considering a traditional built-up roof, exploring the benefits of single-ply membranes, or investigating cutting-edge sustainable options, professional guidance ensures you navigate the complexities of commercial roofing systems successfully. Contact our team today to begin developing the optimal roofing strategy for your commercial property.